我們在數控車床上進行螺紋加工時,通常采用一把刀具進行切削。在加工大螺距螺紋時,因刀具磨損過快,會造成切削加工后螺紋尺寸變化大、螺紋精度低。經過多年的探索,我們摸索出了一種在數控車床上切削加工螺紋時,分粗、精車刀進行。在加工過程中,當粗車刀片磨損到極限后,把精車刀片換到粗車刀具上,精車刀具重新換新刀片。這樣能在保證螺紋切削加工精度的同時,也降低刀具費用。該方法關鍵取決于對粗、精螺紋刀具的對刀精度。
1.操作方法
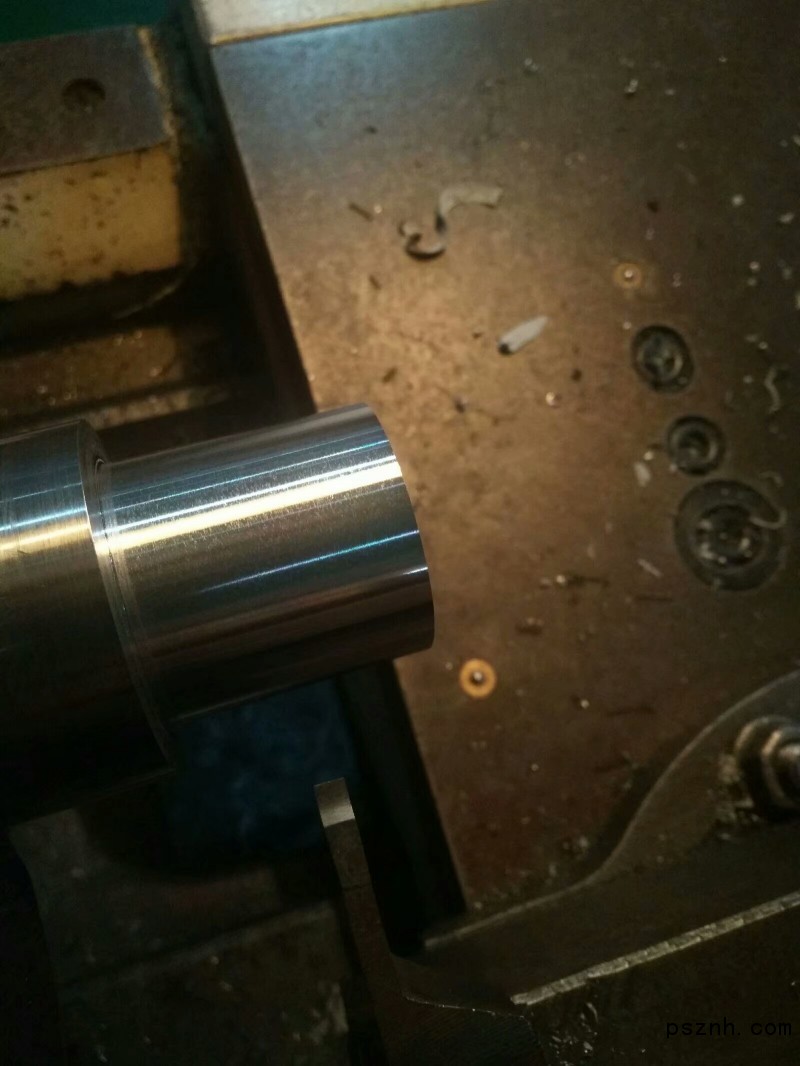
1.操作方法
把工件端面和外圓都切削一刀(端面平,車外圓),然后測量外圓直徑D;換粗車螺紋刀切削螺紋。具體方法如下:
把粗加工刀具(T0x00)用手搖脈沖發生器先對切削加工后的外圓D。用手搖脈沖發生器在Z軸正方向搖出工件,輸入D值(此把刀X軸對刀完)。記下X軸顯示的具體數據。用手搖脈沖發生器在X軸所顯示記錄的數據上向負方向進給1~2mm。同樣用手搖脈沖發生器在Z軸負方向進給,刀具切削到工件即可。輸入Z0(Z軸對刀完)。這時粗車螺紋刀具對刀結束。
按此方法再對螺紋精加工,操作步驟和粗車刀具對刀方法完全一致。這樣就不會在切削過程中產生亂扣現象。即使有更多把刀具切削加工,也同樣不會產生亂扣現象。
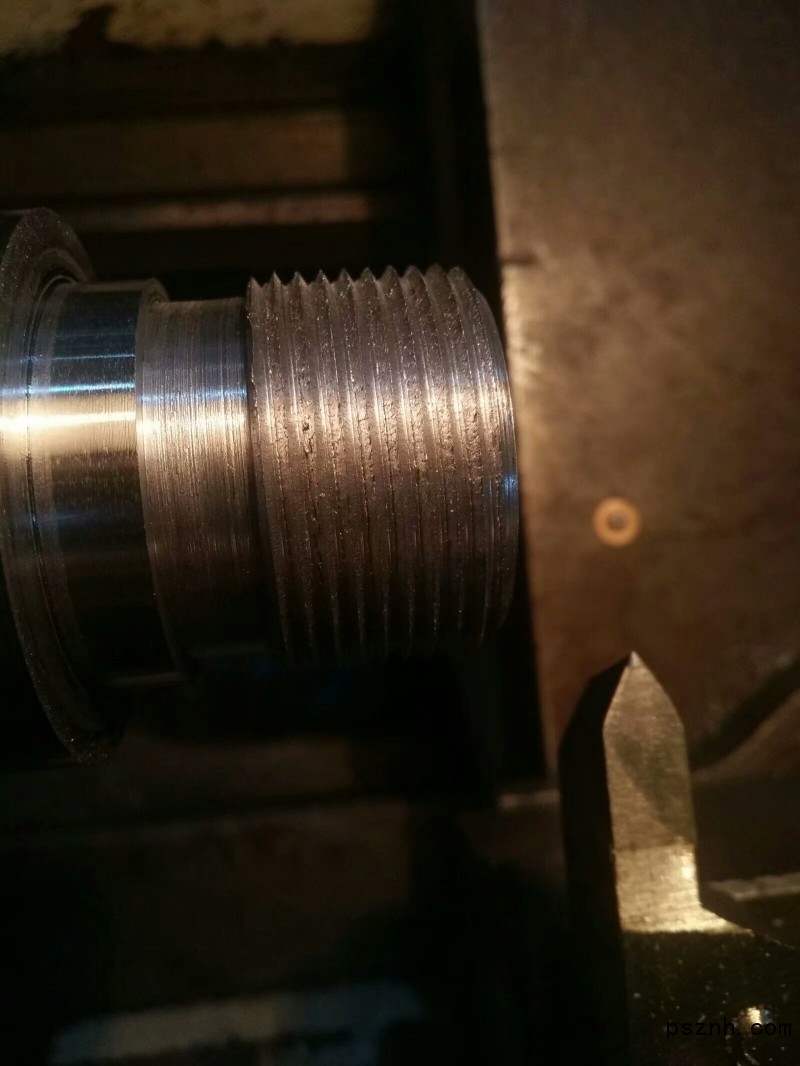
2.注意事項
(1)各把刀具在對X軸時,機床顯示的數字各不相同。一定要記錄好各把刀具的實際數據。在退出X軸后,多把螺紋切削刀具X軸進刀的數據一定要相同,不能有差異。
(2)在對刀的過程中,接近工件X軸和Z軸時,建議手搖脈沖發生器最好選擇進給量0.001mm擋位。
(3)、車削臺階軸時,為了保證車削時的剛性,一般應先車直徑較大的部分,后車直徑較小的部分。
(4)、在軸得工件上切槽時,應在精車之前進行,以防止工件變形。
(5)、精車帶螺紋的軸時,一般應在螺紋加工之后再精車無螺紋部分。
(6)、鉆孔前,應將工件端面車平。必要時應先打中心孔。
(7)、鉆深孔時,一般先鉆導向孔。
(6)、車削(Φ10—Φ20)㎜的孔時,刀桿的直徑應為被加工孔徑0.6—0.7倍;加工直徑大于Φ20㎜的孔時,一般應采用裝夾刀頭的刀桿。
(8)、車削多頭螺紋或多頭蝸桿時,調整好交換齒輪后要進行試切。
(9)、使用自動車床時,要按機床調整卡片進行刀具與工件相對位置的調整,調好后要進行試車削,首件合格后方可加工;加工過程中隨時注意刀具的磨損及工件尺寸與表面粗糙度。
(10)、在立式車床上車削時,當刀架調整好后,不得隨意移動橫梁。
(11)、當工件的有關表面有位置公差要求時,盡量在一次裝夾中完成車削。
(12)、車削圓柱齒輪齒坯時,孔與基準端面必須在一次裝夾中加工。必要時應在該端面的齒輪分度圓附近車出標記線。